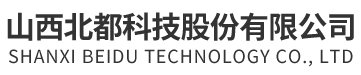
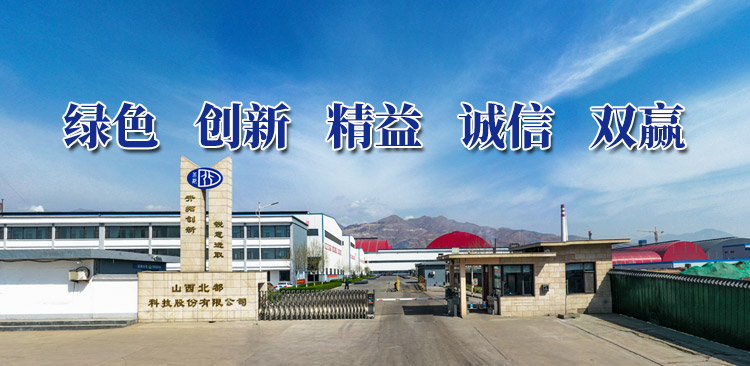

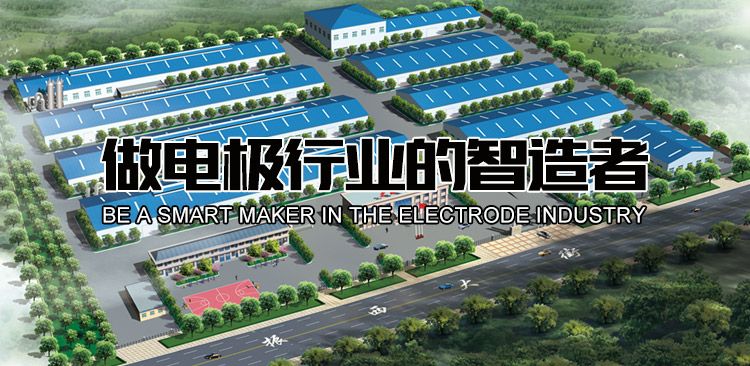
炭素知識課堂:各同向性的等靜壓石墨生產工藝簡介
編輯:2023-11-13 15:58:37
什么是等靜壓石墨
耐熱性好,在惰性氣氛下,隨溫度的升高其機械強度升高,在2500℃左右時達到*大值; 與普通石墨相比,均勻性好,而且結構精細致密; 熱膨脹系數低,抗熱震性能好; 各向同性,在各個方向上性能一致; 耐化學腐蝕性強,能經受住熔融金屬和玻璃的滲透侵蝕; 導電性、導熱性良好; 具有優異的機械加工性能,幾乎可以加工成任意形狀的物品。
石墨成型方法
基本定義
擠壓成型的材料壓坯組織結構
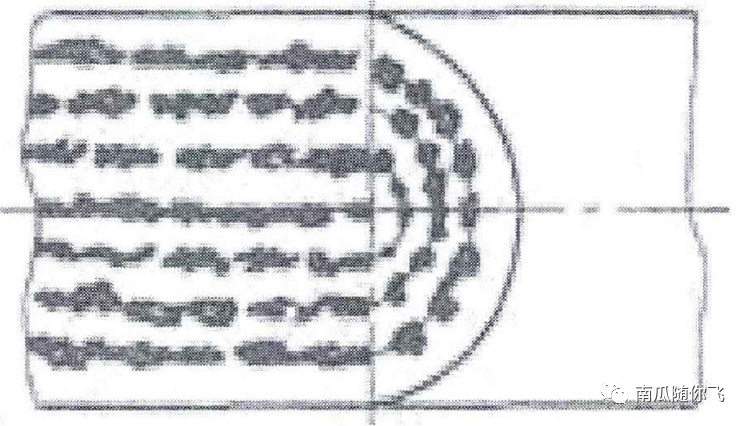
擠壓成型材料壓坯的體積密度分布
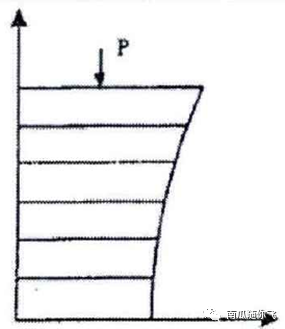
2. 模壓成型
基本定義
模壓成型的材料壓坯組織結構
模壓成型材料壓坯的體積密度分布
3. 等靜壓成型
基本定義
等靜壓成型的材料壓坯組織結構
等靜壓成型時壓粉被置于模具內,模具外的液體或氣體以相同的壓力作用在模具上,并傳遞到物料上,使物料從周圍向中心密實,顆粒的運動主要為平動。各方向上的力相等,粒子不產生轉動。粒子在裝料時處于雜亂無序狀態,密實后仍然處于雜亂狀態。故不出現規律性的層狀分布結構如下圖所示。
模壓成型材料壓坯的體積密度分布
等靜壓技術的特點
等靜壓成型的制品密度高,比單向和雙向模壓成型高5%-15%,熱等靜壓制品相對密度可達99.8%-99.99%。 壓壞密度均勻一致。在摸壓成型中,無論是單向、還是雙向壓制,由于粉料與鋼膜之間的摩擦力,會導致壓壞密度分布不均。這種密度的變化在壓制復雜形狀制品時,往往可達到10%以上。等靜壓流體介質傳遞壓力,各向相等。包套與粉料受壓縮大體一致,粉料與包套無相對運動,彼此之間的摩擦阻力少,壓力只有輕微地下降,這種密度下降梯度一般只有1%以下,因此,可認為坯體密度是均勻的。 密度均勻。制作長徑比不受限制,有利于生產棒狀、管狀、細長產品。 等靜壓成型工藝,一般不需要在粉料中添加潤滑劑,減少了對制品的污染,簡化了制造工序。 等靜壓成型的制品,性能優異,生產周期短,應用范圍廣。
等靜壓石墨材料的特點
液體或氣體加壓,成型壓力高,可以壓制大尺寸制品。壓粉用橡膠、塑料、玻璃或金屬模具裝著,密封后置于液體或氣體中加壓,制品表面在均勻受壓的條件下等比例收縮,生坯密度大。可壓制大規格制品。 可選擇保壓時間以及控制泄壓速度,釋放壓力后制品彈性后效小,使壓制超細結構產品難度降低,不會因彈性后效太大出現壓坯開裂現象(冷模壓制品會因彈性后效大而出現壓坯開裂現象)。 可以壓制異形制件。改變模具形狀直接壓制成異形坯。
等靜壓石墨材料的特點
1. 各向同性
各向同性石墨材料各方向性能比1.0-1.1; 準各向同性石墨材料各方向性能比1.1-1.2; 各向異性石墨材料各方向性能比大于1.2;
3. 細結構
等靜壓石墨材料的生產工藝流程
1. 原料及破碎
2. 配料及混捏
3. 成型
對于體積密度要求較高的石墨制品,焙燒的過程中容易產生裂紋廢品,因此要用較為緩慢的升溫曲線。對于較小尺寸石墨產品的焙燒,可以用耐熱材料做成方形或圓形的容器,然后將生制品放在容器中并加入填充料隔離和覆蓋,再裝到焙燒爐中進行焙燒。
浸漬的關鍵在于浸透,高密度石墨制品要經2-4次浸漬,每次浸漬后均需要焙燒一次。對于浸漬來說,應該正確地選擇浸漬劑的軟化點(關系到浸漬劑的粘度),還要控制好焙燒品浸漬前的預熱溫度及浸漬罐的溫度、壓力、真空度、加壓時間等工藝參數,以達到*佳的浸漬*。
反復浸漬、焙燒工藝處理周期長,一般在2-3個月左右,對設備的使用壽命提出了較高的要求,同時也增加了人力和物力的投入。
5. 石墨化和提純處理
(來源鏈接:https://mp.weixin.qq.com/s/2R0gP5D1PgAAaP_AL7xsuQ)
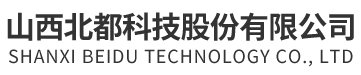
服務熱線:0359-5668082
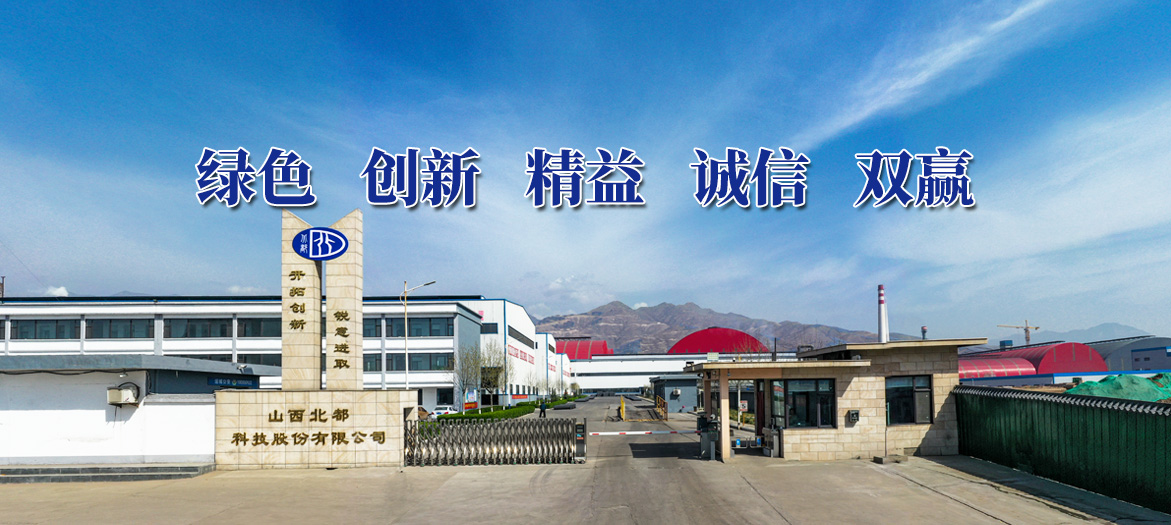
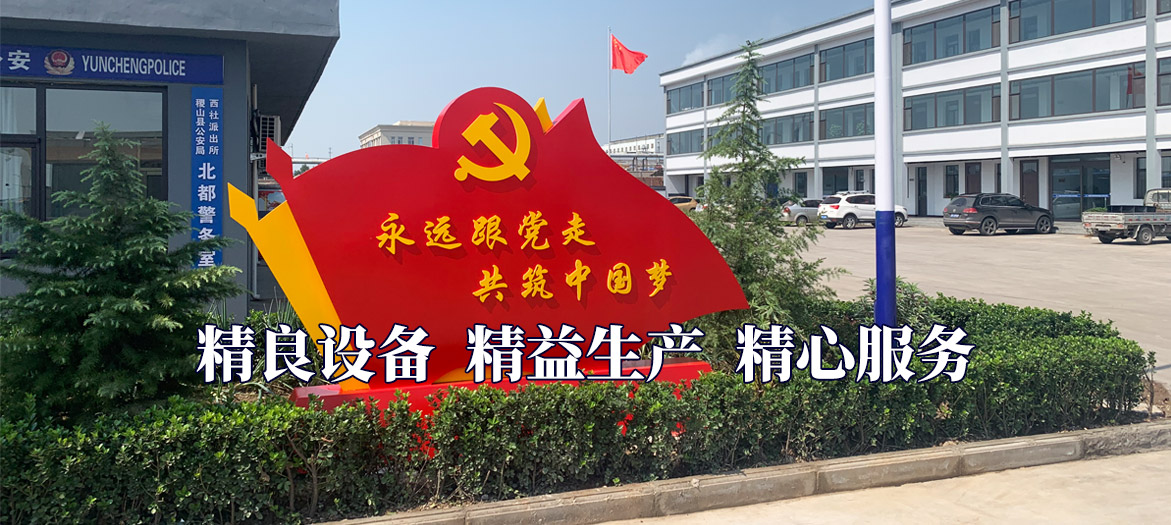
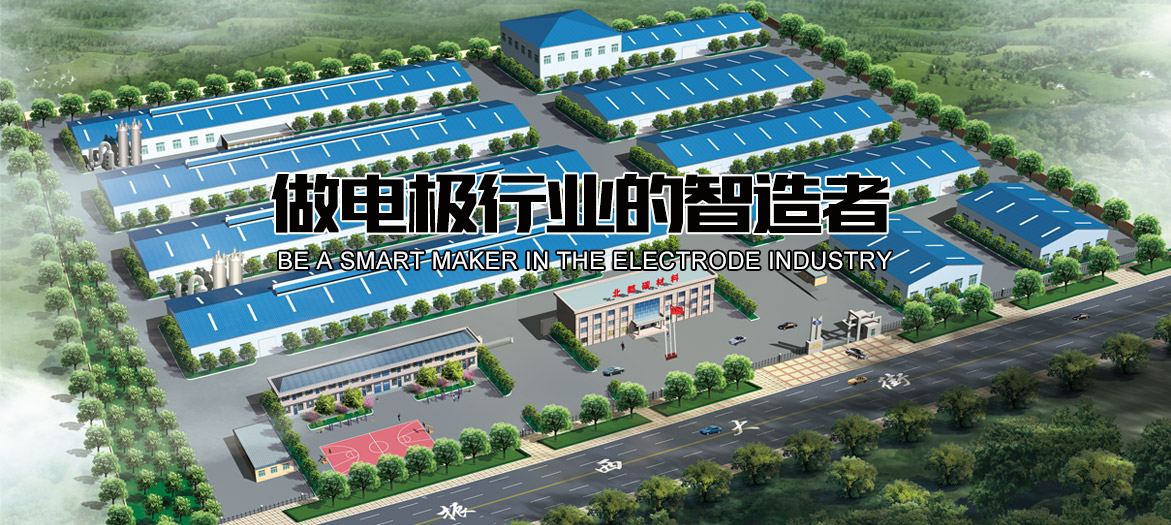
文章詳情 DETAILS
文章詳情 DETAILS
炭素知識課堂:各同向性的等靜壓石墨生產工藝簡介
編輯:2023-11-13 15:58:37
什么是等靜壓石墨
耐熱性好,在惰性氣氛下,隨溫度的升高其機械強度升高,在2500℃左右時達到*大值; 與普通石墨相比,均勻性好,而且結構精細致密; 熱膨脹系數低,抗熱震性能好; 各向同性,在各個方向上性能一致; 耐化學腐蝕性強,能經受住熔融金屬和玻璃的滲透侵蝕; 導電性、導熱性良好; 具有優異的機械加工性能,幾乎可以加工成任意形狀的物品。
石墨成型方法
基本定義
擠壓成型的材料壓坯組織結構
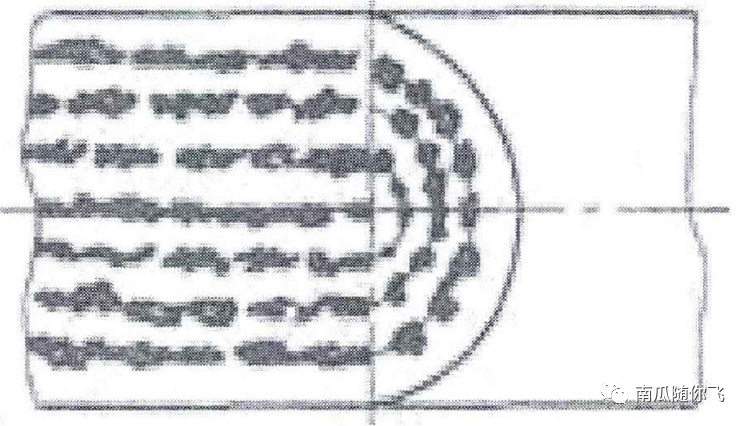
擠壓成型材料壓坯的體積密度分布
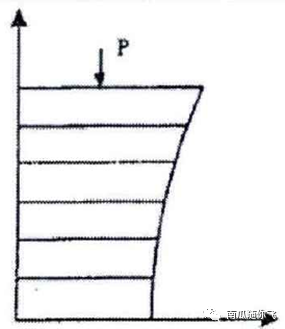
2. 模壓成型
基本定義
模壓成型的材料壓坯組織結構
模壓成型材料壓坯的體積密度分布
3. 等靜壓成型
基本定義
等靜壓成型的材料壓坯組織結構
等靜壓成型時壓粉被置于模具內,模具外的液體或氣體以相同的壓力作用在模具上,并傳遞到物料上,使物料從周圍向中心密實,顆粒的運動主要為平動。各方向上的力相等,粒子不產生轉動。粒子在裝料時處于雜亂無序狀態,密實后仍然處于雜亂狀態。故不出現規律性的層狀分布結構如下圖所示。
模壓成型材料壓坯的體積密度分布
等靜壓技術的特點
等靜壓成型的制品密度高,比單向和雙向模壓成型高5%-15%,熱等靜壓制品相對密度可達99.8%-99.99%。 壓壞密度均勻一致。在摸壓成型中,無論是單向、還是雙向壓制,由于粉料與鋼膜之間的摩擦力,會導致壓壞密度分布不均。這種密度的變化在壓制復雜形狀制品時,往往可達到10%以上。等靜壓流體介質傳遞壓力,各向相等。包套與粉料受壓縮大體一致,粉料與包套無相對運動,彼此之間的摩擦阻力少,壓力只有輕微地下降,這種密度下降梯度一般只有1%以下,因此,可認為坯體密度是均勻的。 密度均勻。制作長徑比不受限制,有利于生產棒狀、管狀、細長產品。 等靜壓成型工藝,一般不需要在粉料中添加潤滑劑,減少了對制品的污染,簡化了制造工序。 等靜壓成型的制品,性能優異,生產周期短,應用范圍廣。
等靜壓石墨材料的特點
液體或氣體加壓,成型壓力高,可以壓制大尺寸制品。壓粉用橡膠、塑料、玻璃或金屬模具裝著,密封后置于液體或氣體中加壓,制品表面在均勻受壓的條件下等比例收縮,生坯密度大。可壓制大規格制品。 可選擇保壓時間以及控制泄壓速度,釋放壓力后制品彈性后效小,使壓制超細結構產品難度降低,不會因彈性后效太大出現壓坯開裂現象(冷模壓制品會因彈性后效大而出現壓坯開裂現象)。 可以壓制異形制件。改變模具形狀直接壓制成異形坯。
等靜壓石墨材料的特點
1. 各向同性
各向同性石墨材料各方向性能比1.0-1.1; 準各向同性石墨材料各方向性能比1.1-1.2; 各向異性石墨材料各方向性能比大于1.2;
3. 細結構
等靜壓石墨材料的生產工藝流程
1. 原料及破碎
2. 配料及混捏
3. 成型
對于體積密度要求較高的石墨制品,焙燒的過程中容易產生裂紋廢品,因此要用較為緩慢的升溫曲線。對于較小尺寸石墨產品的焙燒,可以用耐熱材料做成方形或圓形的容器,然后將生制品放在容器中并加入填充料隔離和覆蓋,再裝到焙燒爐中進行焙燒。
浸漬的關鍵在于浸透,高密度石墨制品要經2-4次浸漬,每次浸漬后均需要焙燒一次。對于浸漬來說,應該正確地選擇浸漬劑的軟化點(關系到浸漬劑的粘度),還要控制好焙燒品浸漬前的預熱溫度及浸漬罐的溫度、壓力、真空度、加壓時間等工藝參數,以達到*佳的浸漬*。
反復浸漬、焙燒工藝處理周期長,一般在2-3個月左右,對設備的使用壽命提出了較高的要求,同時也增加了人力和物力的投入。
5. 石墨化和提純處理
(來源鏈接:https://mp.weixin.qq.com/s/2R0gP5D1PgAAaP_AL7xsuQ)
版權所有:山西北都科技股份有限公司 備案號:晉ICP備2022006699號-1